1909
Henrik Johan Henriksen and Waldemar Kähler establish the joint gravel pit enterprise ‘Singelsforretningen Omø’. The business employs 20 people who are each paid a salary of DKK 3 per day for their hard work.
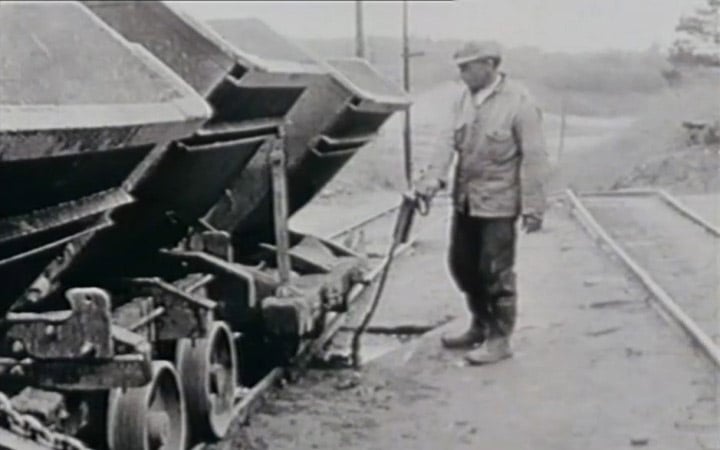
1937
After completing his studies in the United States, Henrik Johan Henriksen’s oldest son, Finn Henriksen, returns to Denmark with the production rights to stone wool in Scandinavia and Germany. The company commences production of Rockwool in Hedehusene, Denmark, followed by Sweden, Norway, and Germany. Through the Rockwool partnership in Sweden, a new building material called ‘aircrete’ is discovered and production of aircrete commences at the calcium silicate factory in Ølsted, Denmark.
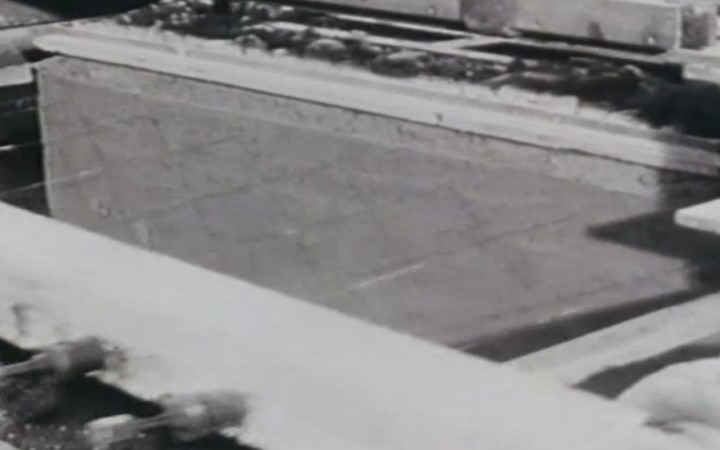
1958
The company enters the UK through the acquisition of 50% of the share capital in the British company, Celcon Limited, with the aim of producing aircrete in the UK using Danish know-how.
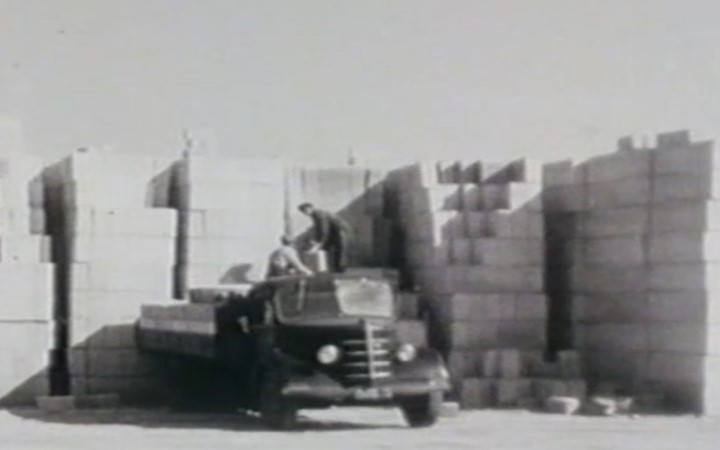
1962
The Rockwool activities are divided from the other activities. The Henriksen family consolidates its businesses under one company called Henriksen & Henriksen I/S and a number of sales companies called H+H-Stenindustrier A/S, H+H-Gasbeton A/S, and H+H-Scanbyg A/S. The company becomes the majority shareholder of Celcon Limited with a 51% ownership.
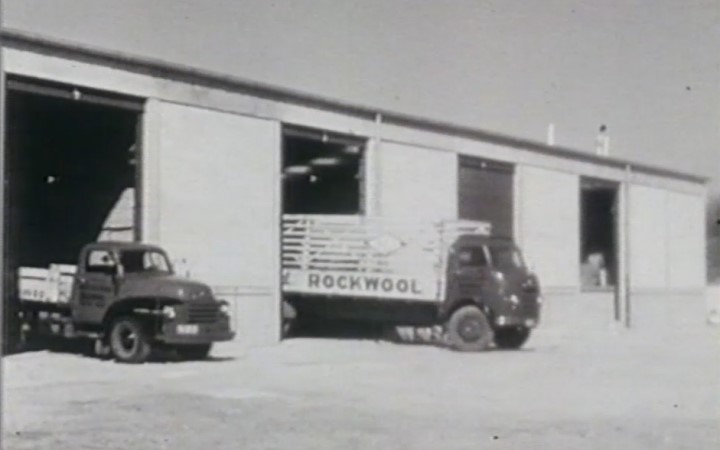
1985
In late-1984, it is decided that the company’s B-shares are to be listed on the Copenhagen Stock Exchange. The IPO takes place in June 1985 and the company raises DKK 68 million of capital. The aim of the listing is to raise capital for the diversification of activities in Denmark, including the acquisition of a smaller Danish furniture company and a Danish kitchen-element factory. The company continues as a conglomerate until 1998.
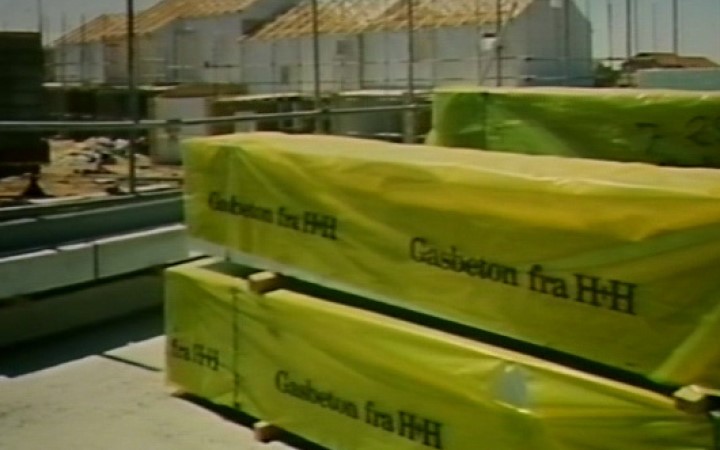
2000
H+H sets out to become a leading wall-building provider through the consolidation of the European markets and focuses its activities around the production of aircrete. H+H further expands its aircrete activities into Finland and Germany.

2005
The geographic expansion continues and H+H enters the Polish aircrete market through the acquisition of five aircrete factories.
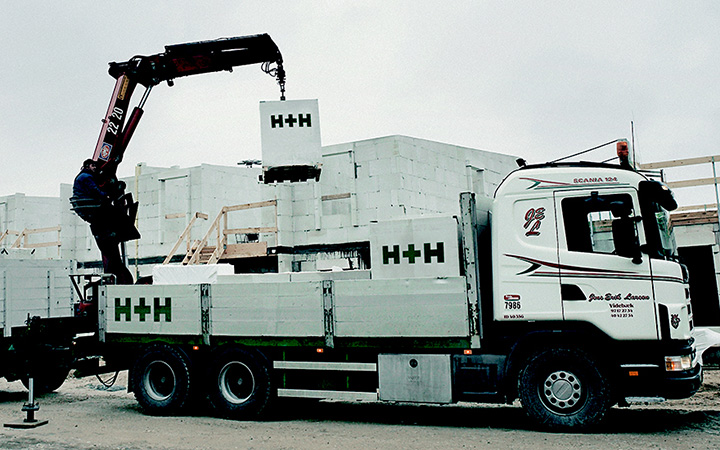
2009
The geographic expansion continues into Russia until the financial crisis of 2008-2009, which takes its toll on the Group, leaving it close to bankruptcy. The parent company is recapitalised and the two share classes are merged into one.
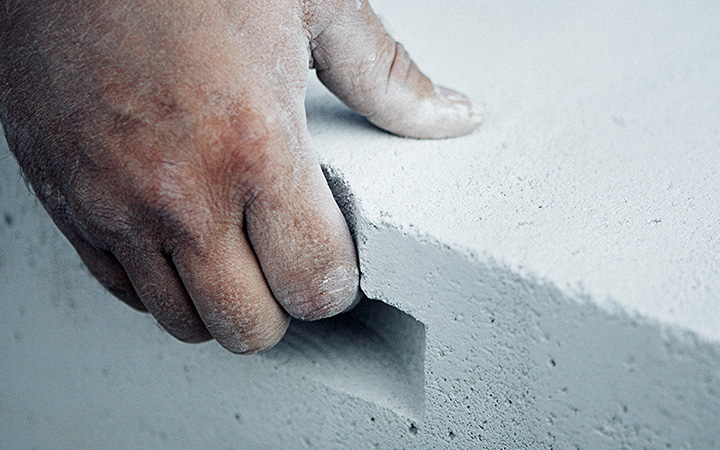
2011
The turnaround of H+H is commenced by streamlining the Group, divesting loss-making activities, and implementing several process improvements across the business.
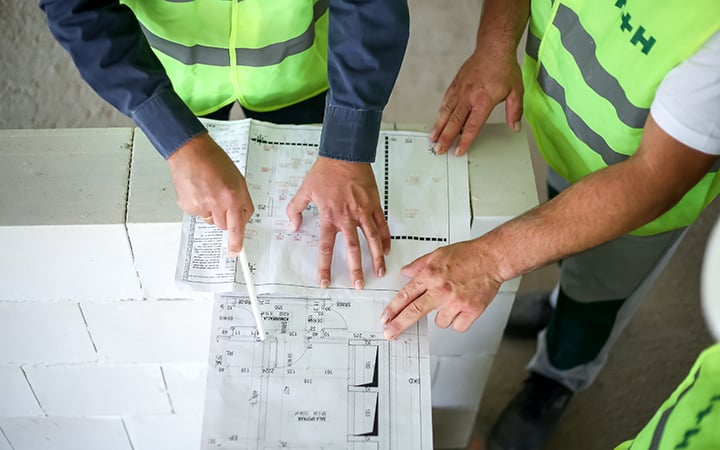
2015
With the business back on track, the company sets its sights on consolidating the European market. First step is the restructuring of the Polish aircrete business through the acquisition of Grupa Prefabet S.A. and the closure of three factories.
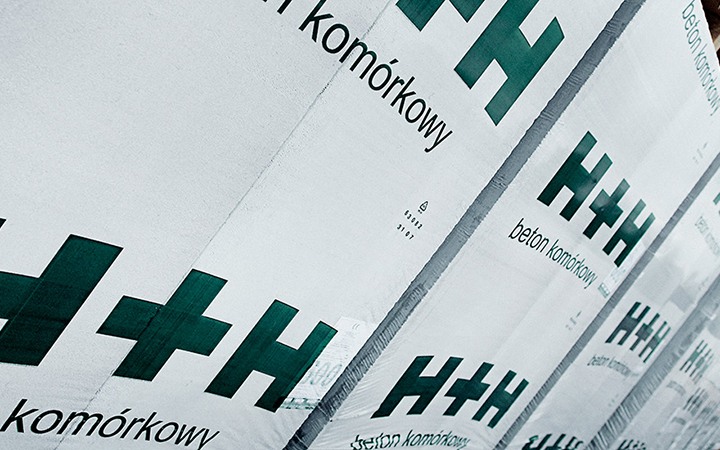
2017
H+H signs agreements to acquire calcium silicate unit businesses in Poland, Germany, and Switzerland. These acquisitions are truly transformational for H+H as they expand the existing product portfolio and create a more balanced footprint for the company. It also creates a strong platform for further market consolidation and provided and entry into the fast-growing high-rise segment.
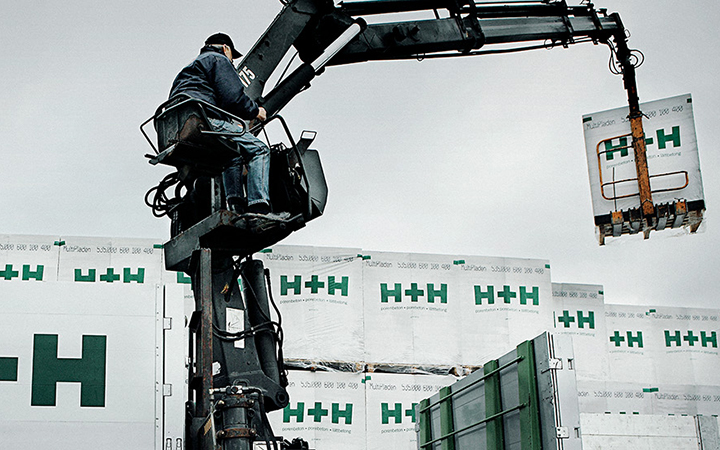
2019
The Group’s Russian activities are divested allowing H+H to focus on the continued development of the core markets of Central Western Europe, the UK, and Poland. An additional CSU plant is acquired in Germany.
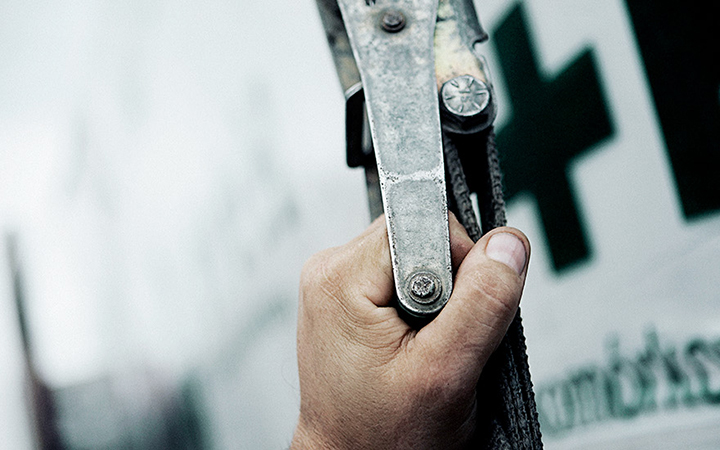
2020
In early-2020, H+H closes the acquisition of the majority shareholding in Porenbetonwerk Laussnitz GmbH & Co. KG, a German AAC unit business. Further, H+H releases its first separate sustainability report which includes the ambitious target of net-zero — and potentially net-negative — carbon emissions from its products and operations by 2050.
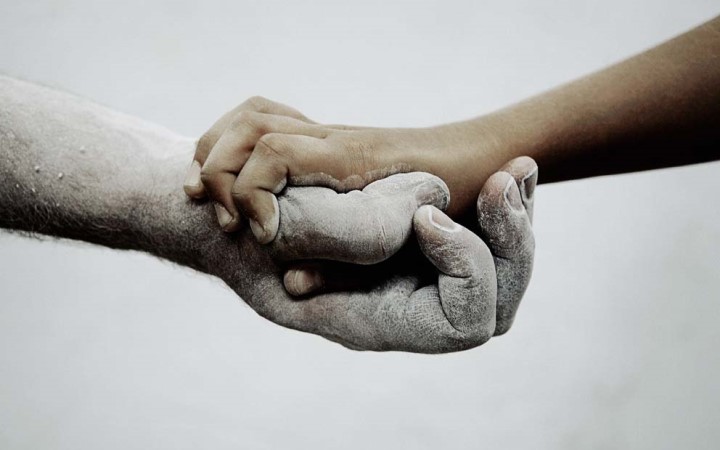
2021
H+H acquires one AAC factory and one combined AAC and CSU factory in Germany. This is yet another important step on H+H’s ongoing growth journey and the restructuring of the German white-stone market.
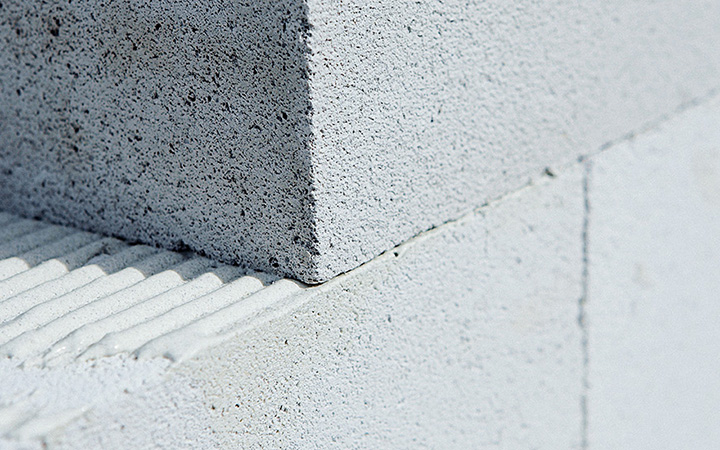
2022
In 2022, H+H delivers the best result ever with an organic growth of 14% and an EBIT before special items of DKK 455 million.
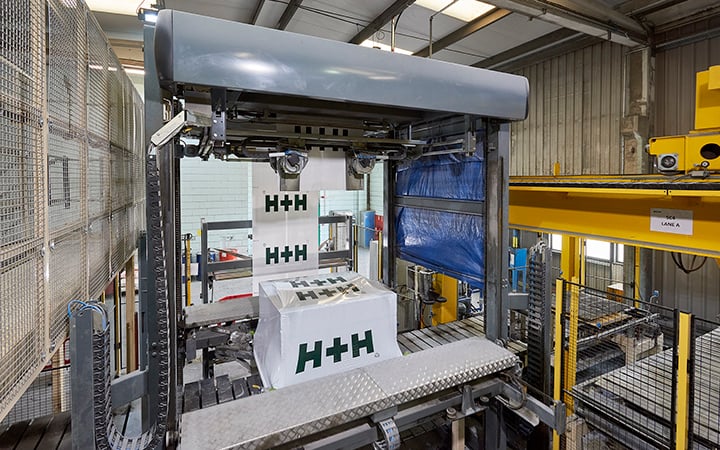
2023
Macroeconomic and political turmoil in Europe sends the market into a crisis. H+H responds by initiating a business improvement program focusing on plant network efficiency, SG&A cost savings and optimising procurement efforts. 5 plants are permanently closed, while 4 others are temporarily taken out of production.